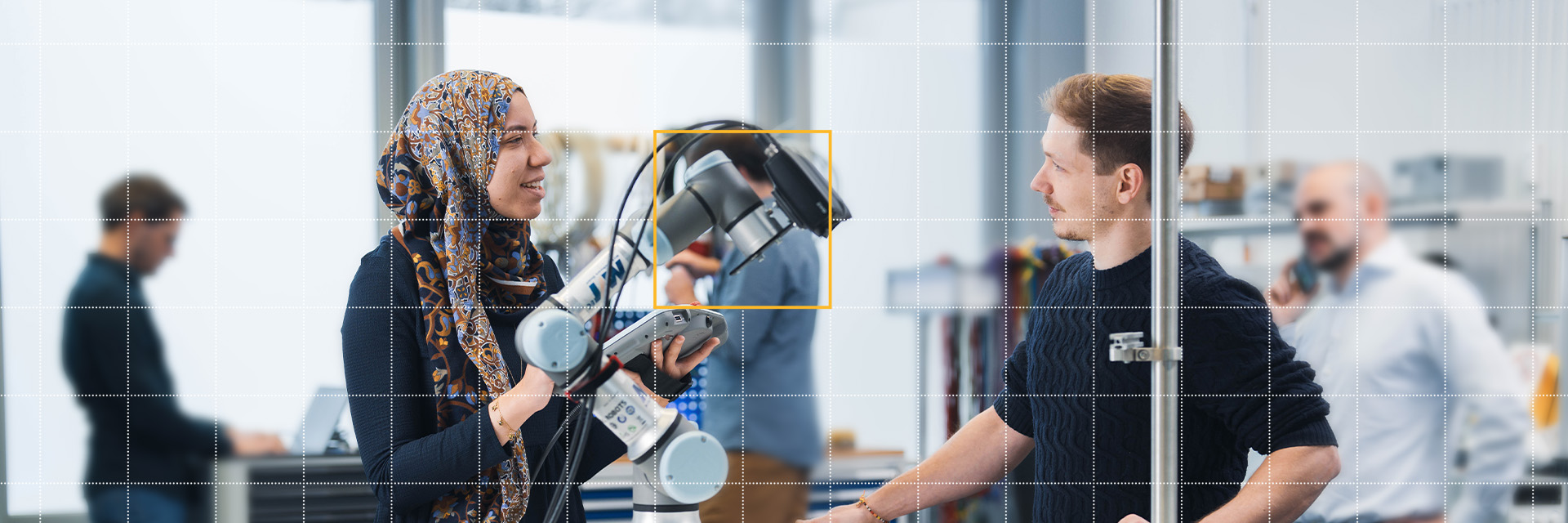
Machine Vision automates and optimizes battery inspection
Battery Production | HALCON | Blob Analysis | InspectionA variety of defects can occur during battery production. Averna has developed a method for the automated inspection of batteries that reliably detects all conceivable defects. Here, the machine vision software MVTec HALCON plays a key role.
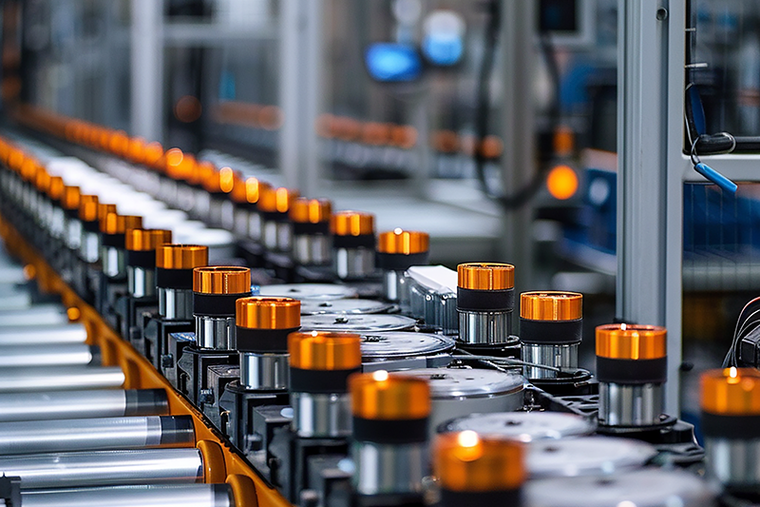
Battery manufacturers must meet very high-quality standards in their production processes. This applies to all types of batteries, whether for consumer electronics, electric vehicles, or other applications. Battery production is a very complex process. At the end of this process, there is a comprehensive testing workflow that takes place during the so-called forming and aging process. Here, the battery is not only tested for functionality, but also inspected for external defects such as deformations, indentations, or scratches. The defects that can occur here can vary greatly, both in shape and size. An enormous challenge is to precisely detect all these anomalies as part of the quality inspection. This is the only way to screen out defective batteries reliably before they leave the factory.
Optimizing battery inspection and reducing costs
The Canadian company Averna has designed, developed, and implemented a sophisticated solution for quality inspection on behalf of a well-known battery manufacturer to address this complex challenge. This solution can be used to identify a wide range of external product defects and locate them precisely. The aim of the project was to significantly improve battery inspection and thus quality, increase customer satisfaction, and reduce overall costs. “Speed was the top priority for this application because production processes must not be delayed by a time-consuming screening procedure,” says Roel Geraerts, Team Leader Vision at Averna, thus defining a key requirement. Further challenges were the varying shapes and sizes of the batteries, as well as the wide range of potential defects that can occur during battery production.
Pushing the pace of quality inspection
There was also another requirement: previously, the finished batteries were first labeled and only then inspected for defects as part of the quality inspection. This meant that production defects were often hidden by the label and therefore overlooked. Hence, also low-quality products could be delivered to customers. The new solution had to be capable of inspecting batteries very quickly and reliably detecting all conceivable damage. This had to take place before the labeling process to ensure that only fault-free products were labeled and released for shipment.
High-performance systems for lighting and machine vision were required
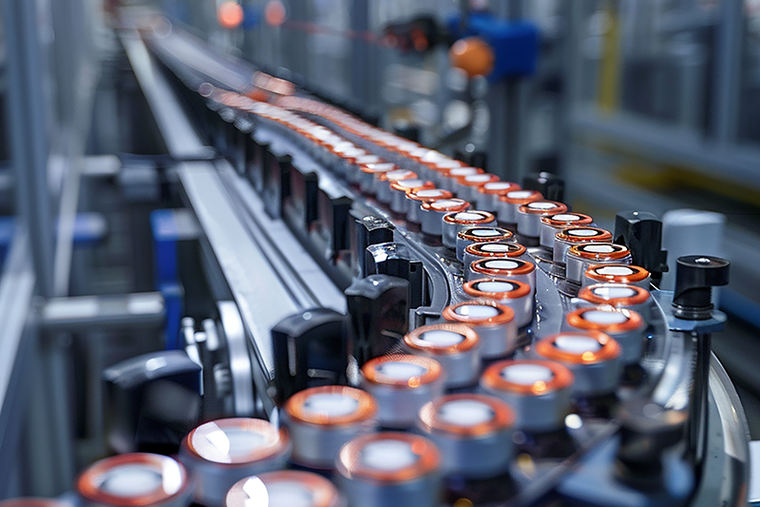
“Our best option for achieving the necessary speed and high level of automation for the inspection workflow was a professional machine vision solution,” explains Geraerts. Since the batteries are inspected from all sides in a 360-degree perspective, powerful technologies for lighting and handling were required. So, the specialists at Averna worked closely with the customer to design a sophisticated solution consisting of high-quality cameras and lighting systems mounted on a conveyor belt. Powerful light beams are directed onto the battery at optimal angles to make even the smallest discrepancies on the body visible during the battery inspection. By capturing a large number of images at a very high speed, the position of the test object can be quickly detected and electronically communicated. Several batteries can be seen in each image, so that the required inspection time can be reduced to a minimum by viewing them simultaneously. In this process, several cameras precisely capture every angle of the battery, generating almost 10,000 images per minute.
Highly precise image analysis with MVTec HALCON
The machine vision software MVTec HALCON is seamlessly integrated into Averna's own software and analyzes the images with the highest precision. The combinations of light and shadow and the resulting high contrasts in the image are evaluated using blob analysis. The technology extracts features from connected pixels that share the same logical state, such as color value (blobs). The decisive advantage is the very high processing speed. Within a very short time, the relevant area of the image (region of interest) and then possible anomalies are identified. The battery is then either rejected as defective or – if it is found to be in working order – passed on for labeling. Using a high-speed digital I/O system, the inspection results can be communicated to the control system and the parts automatically sorted, optimizing the quality inspection.
Machine vision ensures fast battery inspection
MVTec HALCON runs Averna's inspection software on a real-time engine, ensuring stable image data recording and evaluation. This makes it possible to automatically eject defective products in a timely manner, even at high speeds. With the help of MVTec HALCON, Averna developed an easy-to-use, customized system that includes fiducial markers. These allow the sharpness, brightness, positioning, and angle of the cameras to be measured exactly for a wide range of purposes, enabling the customer to easily and independently calibrate the system. Thanks to the fiducial markers, such control stations can also be set up identically at other locations in a short time, guaranteeing consistent, company-wide results during battery inspection.
Battery manufacturer benefits from fast and robust quality inspection
“With advanced technologies like blob analysis, MVTec HALCON plays a decisive role in providing our customers with an innovative testing and quality assurance solution. The battery manufacturer benefits not only from high-speed quality inspection, but also from a very robust success rate in the automatic detection of a wide range of defects with different sizes and shapes,” summarizes Roel Geraerts.
Averna is an MVTec Certified Integration Partner.
All product names, trademarks, and images of the products/trademarks are copyright by their holders. All rights reserved.